How To Stop Wasting Time In Package Loading For Last-Mile Delivery
October 25, 2024
When it comes to the logistics of last-mile delivery, our research has found that workers spend nearly 80 percent of their time “searching” in the delivery station or sort center. Not only is the amount of time spent on searching a tremendous waste of human resources, it’s also a major cause of lost, damaged, or expired goods in package delivery.
We describe “searching” as any activity that involves workers looking for the item intended for customer delivery and then making sure it’s placed in the correct vehicle for that delivery. To be specific, searching involves the following:
- Finding the required package or product for delivery
- Finding the required location, e.g., container, vehicle, or specific position
- Undertaking various actions to help find the package, product, or storage location
- Undertaking remedial actions to correct mistakes in the searching process
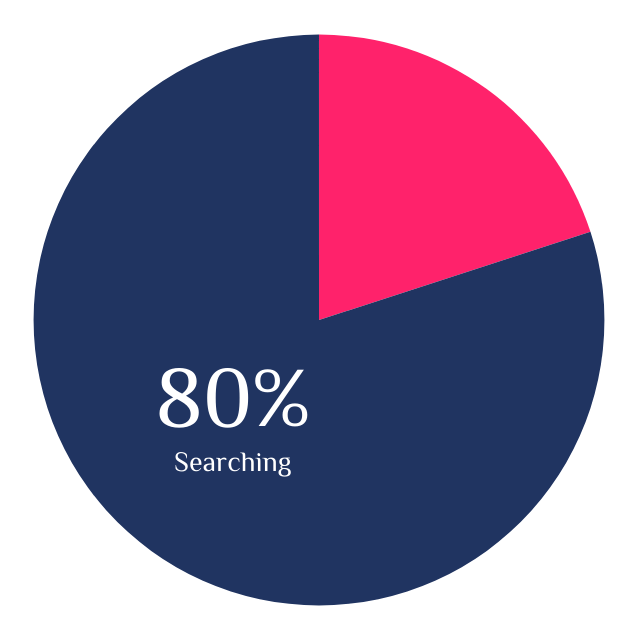
By way of comparison, the time spent moving goods in a last-mile delivery facility accounts for less than 20 percent of the total time.
Although it may be difficult for many in the package delivery industry to accept the fact that 80 percent of the workers time in a facility is wasted on searching, our research here at Lotwork has proven that to be case.
Why Searching Is Not Fundamental To The Delivery Operation
Why Searching Is Not Fundamental To The Delivery Operation
If you apply a First Principles analysis to the operation of a delivery station and sort center, you’ll recognize that searching is not really essential to the fundamental task at hand. If you’re not familiar with the First Principles concept, it’s a method of analysis in which you break down a process to its basic components to determine what’s essential.
The fundamental activities in a package facility for last-mile delivery are as follows:
- Unloading the truck or vehicle during inbound delivery
- Moving the designated package or product to the correct location for storage or delivery
- Loading the outbound delivery vehicle for dispatch
Apart from these three essential actions, all other tasks are auxiliary or remedial measures that do not add value to the process.
From a “First Principles” perspective then, other actions in a last-mile package facility are not fundamental and hence waste time. Specifically, they are:
Finding the designated package on the conveyor belt
Finding the correct location for sorting or loading
Undertaking various actions to help locate the correct package
In fact, facility workers often write a big number on the package to make it more convenient for the driver to spot the correct delivery item. But if the worker puts the wrong number on the package by mistake, then the driver won’t get the right package delivered.
The Solution: Wireless Light Tag Technology
What can you do to eliminate “searching” in a facility? You should take advantage of technology for quick package identification.
Lotwork work with GHE Inc. (Go Home Early – last mile delivery solution) has developed an intelligent labeling system that eliminates “searching.” Workers place Hyco wireless light tags on packages that provide audio-visual cues for item identification in seconds. As a result workers don’t have to search around in the sort center or delivery station to find the correct packages for a customer drop-off.
When an inbound delivery takes place at a sort center or delivery station, workers attach a tag to each package. Although the attachment of a tag does take time at the front end of the process, it saves far more time at the back end because workers can now quickly select the correct packages to load the delivery van. In addition, the use of tags makes it easy for the driver to quickly identify the correct customer’s package at a delivery stop.
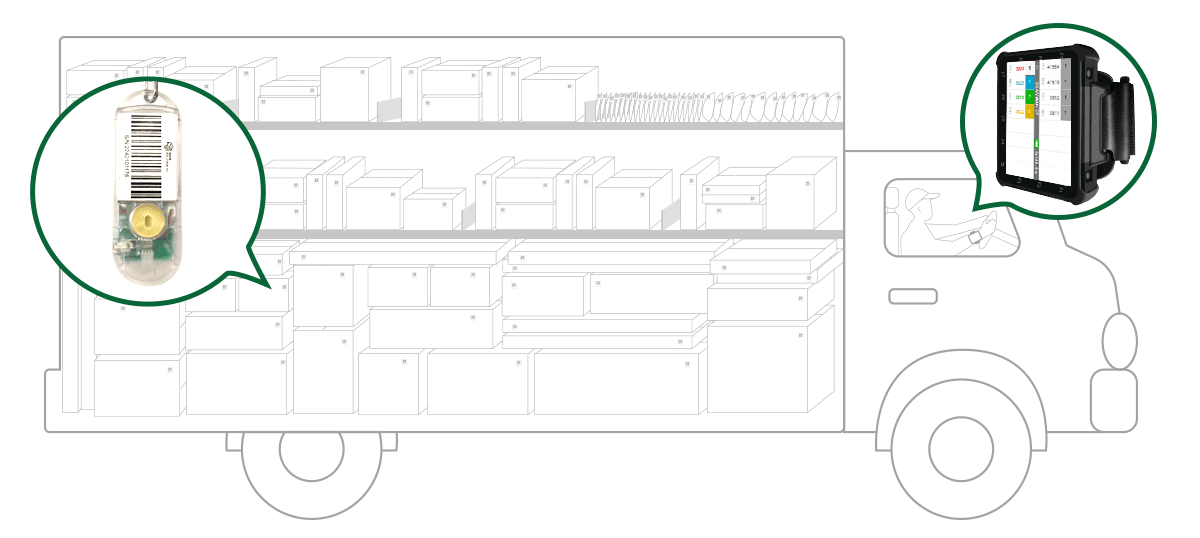
GHE solution
Introducing wireless light tag technology into their facilities gives last-mile and package delivery companies a means to boost productivity by eliminating worker time wasted on “searching.” By saving time, they will maximize labor resources to reduce costs and improve overall operational efficiency.
In fact, facility workers often write a big number on the package to make it more convenient for the driver to spot the correct delivery item. But if the worker puts the wrong number on the package by mistake, then the driver won’t get the right package delivered.