7 Smart Ways to Reduce Picking Errors (Without Slowing Your Team Down)
Gent Ivziku • July 3, 2025
In the world of warehousing and order fulfillment, small mistakes can lead to big headaches — delayed shipments, frustrated customers, and unnecessary costs. But the good news? Picking errors are preventable.
The key is combining the right tools with smarter workflows. Here are seven practical ways to boost accuracy (and keep your team moving fast).
1. Ditch the Handheld Scanner (Try Hands-Free Instead)
Ever fumbled with a scanner while juggling a box? Handheld devices slow pickers down and increase mis-scans. Hands-free options, like ring scanners or wearable computers, let workers scan effortlessly while keeping both hands free.
Tool to Try: Lotwork’s Ring Scanner + Wearable Combo – Scan without stopping, reducing errors by up to 25%.
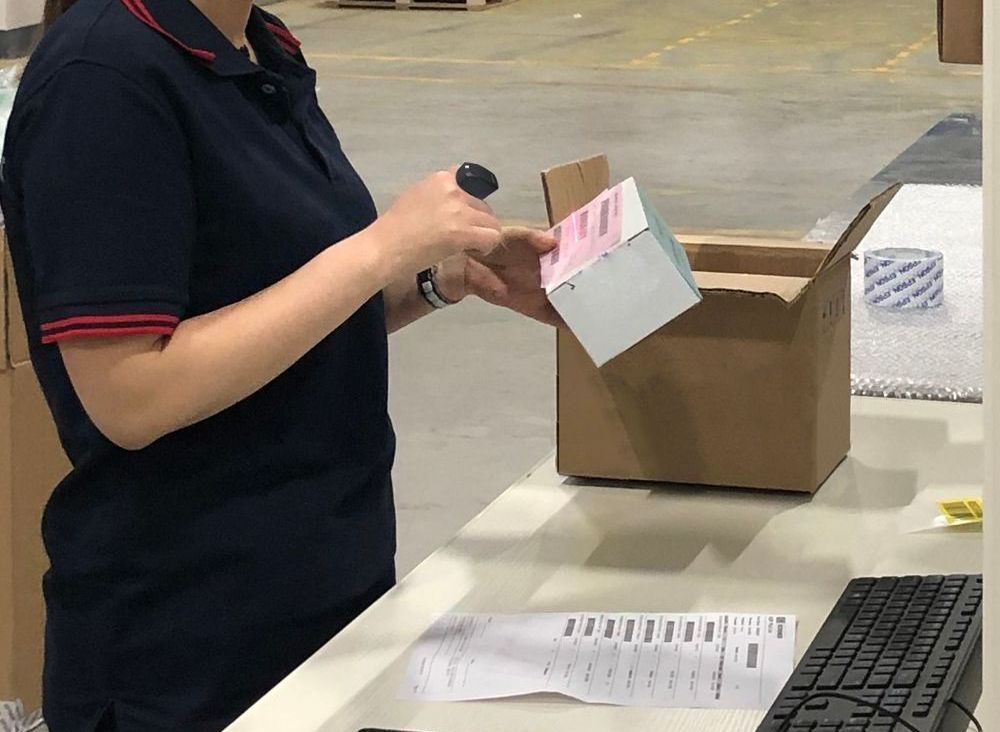
2. Let Lights Guide the Way (Pick-to-Light Systems)
No more squinting at paper lists or guessing locations. Pick-to-Light systems use LED indicators to show exactly where items are, so pickers grab the right thing—every time.
Tool to Try: Lotwork’s Wireless Pick-to-Light – Cuts errors by 35% and speeds up picking by 20%.
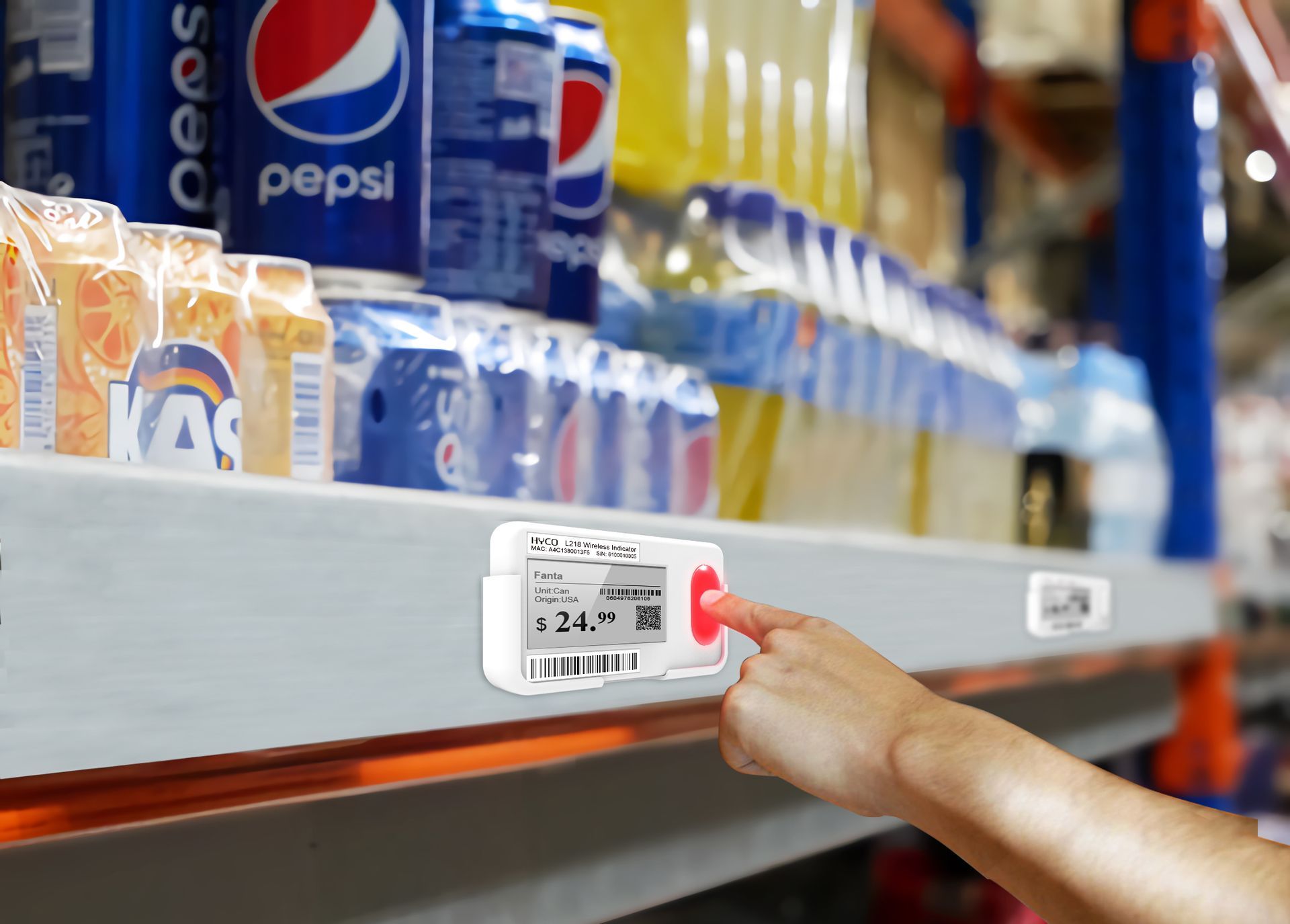
3. Sync Your WMS in Real Time (No More Guessing Games)
If your system lags, mistakes happen. A real-time WMS ensures inventory updates instantly, flags errors immediately, and keeps pickers on track.
Pro Tip: Choose a system that integrates smoothly with your existing software, no IT headaches required.
4. Train Smarter (Not Just Harder)
Even the best tech won’t help if your team isn’t trained well. Regular coaching, digital onboarding, and cross-training ensure everyone stays sharp, especially during busy seasons.
Bonus: Use real-time performance dashboards to give targeted feedback.
5. Organize for the Human Eye (Not Just the System)
Cluttered bins, faded labels, and inconsistent layouts invite mistakes. Standardized storage with clear, scannable labels makes picking intuitive.
Quick Fix: Audit your bins monthly — replace worn labels and adjust placements for better flow.
6. Let Data Reveal Your Weak Spots
Where do most errors happen? Certain SKUs? A specific shift? Data-driven insights help you fix recurring issues before they become costly habits.
Pro tip: Even basic spreadsheets can reveal problem areas if you consistently log errors. The key is reviewing the data regularly, not just collecting it.
7. Turn Accuracy Into a Game (Yes, Really)
People perform better when they’re engaged. Gamify picking accuracy with live leaderboards, small rewards, and team shoutouts.
Easy Win: Post daily top performers — friendly competition works wonders.
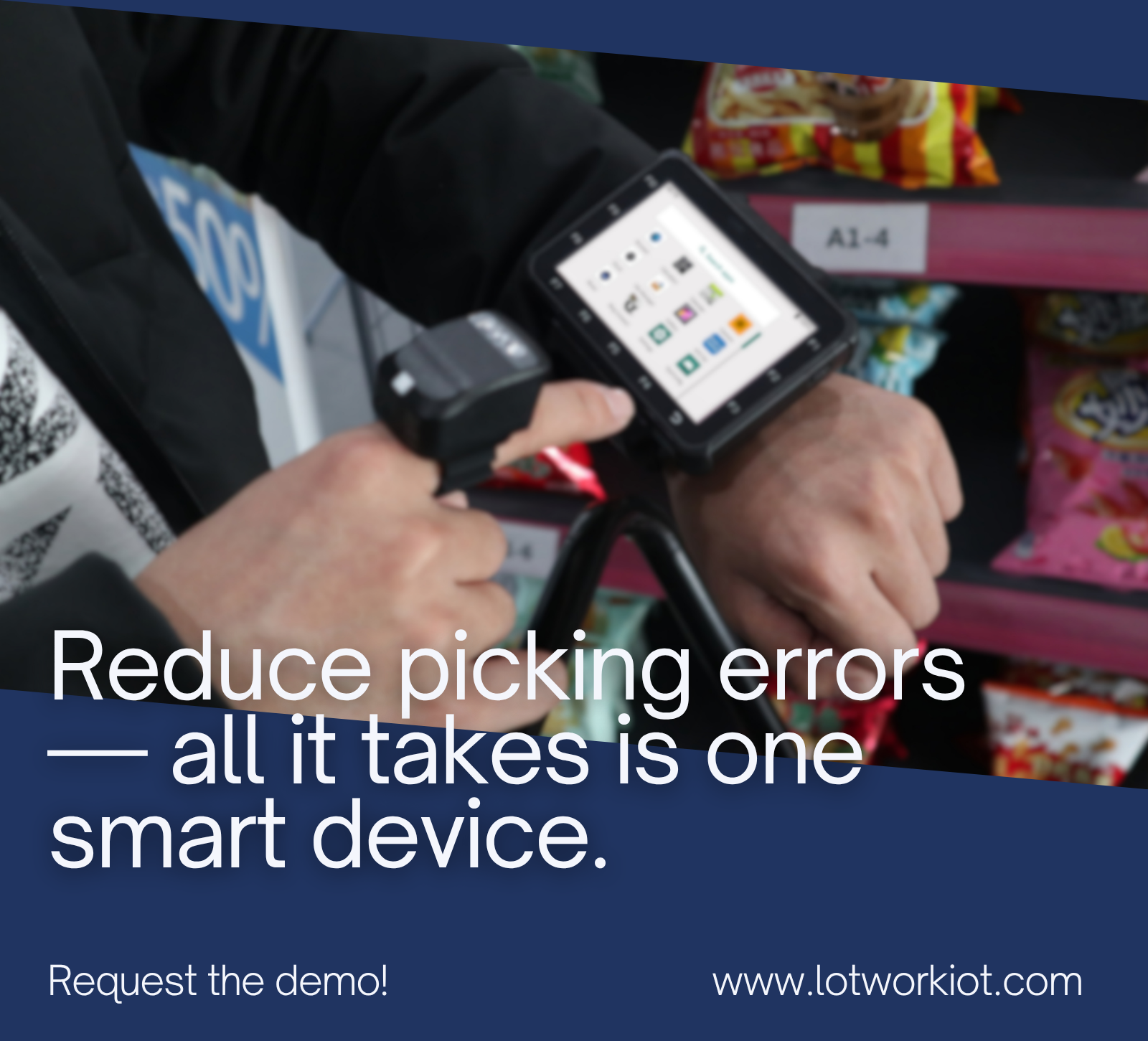
The Bottom Line
Fewer picking errors mean happier customers, fewer returns, and a smoother operation. And the best part? You don’t have to sacrifice speed for accuracy.
Want to see hands-free tech in action?
👉
[Book a Demo] today!
(Which of these strategies could make the biggest impact in your warehouse? Let us know in the comments!)