How Small Companies Can Implement An Effective FEFO Inventory Strategy
October 30, 2024
It’s smart business for companies making or selling perishable goods to employ a First Expired, First Out (FEFO) strategy for inventory management. It ensures that products nearing expiration are prioritized for shipping from the manufacturer's warehouse or distribution center.
This approach to inventory management prevents the risk and economic losses associated with selling expired products. In industries such such as food and pharmaceuticals, FEFO inventory management is critical since expired products pose significant health and even life-threatening risks.
But putting in an effective FEFO strategy requires a complete set of the right technology that often bedevils small companies who can’t afford the expense.
Understanding Effective FEFO Management
To understand what constitutes an effective FEFO inventory management program requires a First Principle analysis. The First Principles concept is a method of analysis in which you break down a process to its basic components to determine what’s essential.
Applying the First Principles approach to FEFO Management finds these are essential actions for an effective program.
- Quickly extracting the expiration information of individual product units
- Storing products in the warehouse at the appropriate location
- Quickly picking and shipping products based on customer order information and expiration data.
Typical FEFO Management Practices In Warehousing
Most warehouses and distribution centers today use a warehouse management system (WMS) to keep track of inventory expiration dates when using a FEFO inventory strategy. Workers collect the product expiration information when the shipment is unloaded or sometimes when the product is placed on the shelves. This is usually done by scanning a barcode on the box or carton to obtain the product expiration dates for the warehouse management software.
But for small companies, in many cases, bar codes are not on the products when received into a warehouse or the information on expiration dates are not encoded into the bar code symbol. Instead the expiration dates are written on the box or package so the worker has to input that information into the computer system. Not only is this method of manual input a slow process, it’s prone to errors.
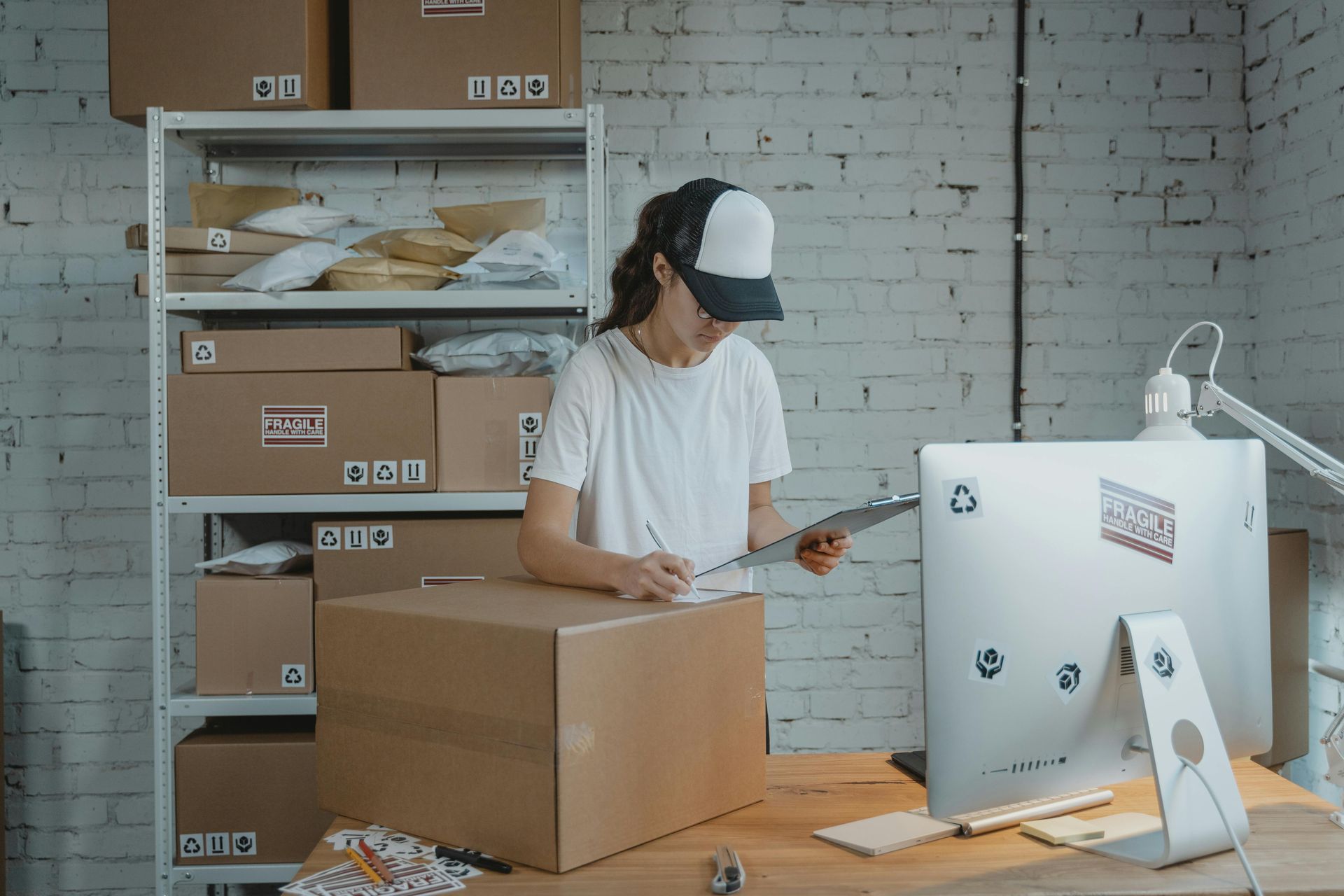
When the time comes to retrieve goods for shipments based on FEFO inventory management, large companies often have some degree of automation to facilitate the process. An automated storage and retrieval system (ASRS) or autonomous mobile robots will convey the product to the picker.
Most small companies can’t afford the huge expense of automation so they still rely on workers to walk through a building to retrieve the products. Even when the WMS provides guidance on product location for retrieval, the picker still have to spend some time looking around in the aisle for the correct item.
A FEFO Technology Solution For Small Companies
Big companies avoid First Principle issues with FEFO inventory management through the use of expensive automation technology. But small companies need affordable technology for effective FEFO. That’s why we at Lotworks have develop our FEFO manager solution.
With our solution, workers are equipped with a wearable computer that has a built-in optical character recognition (OCR) reader. That gives them the ability to scan a box with a written expiration date on it and then send that information to the warehouse management system for tracking. In doing so, they skip having to spend time inputting the information into the computer system.
When it comes time to retrieval, our solution makes the task of picking products easier. Our solution equips racking shelves with light tags that provide a visual and audio signal to a picker for locating the product quickly in the storage area. When the WMS sends a picker down an aisle, that person can immediately spot the location of the product to be acquired.
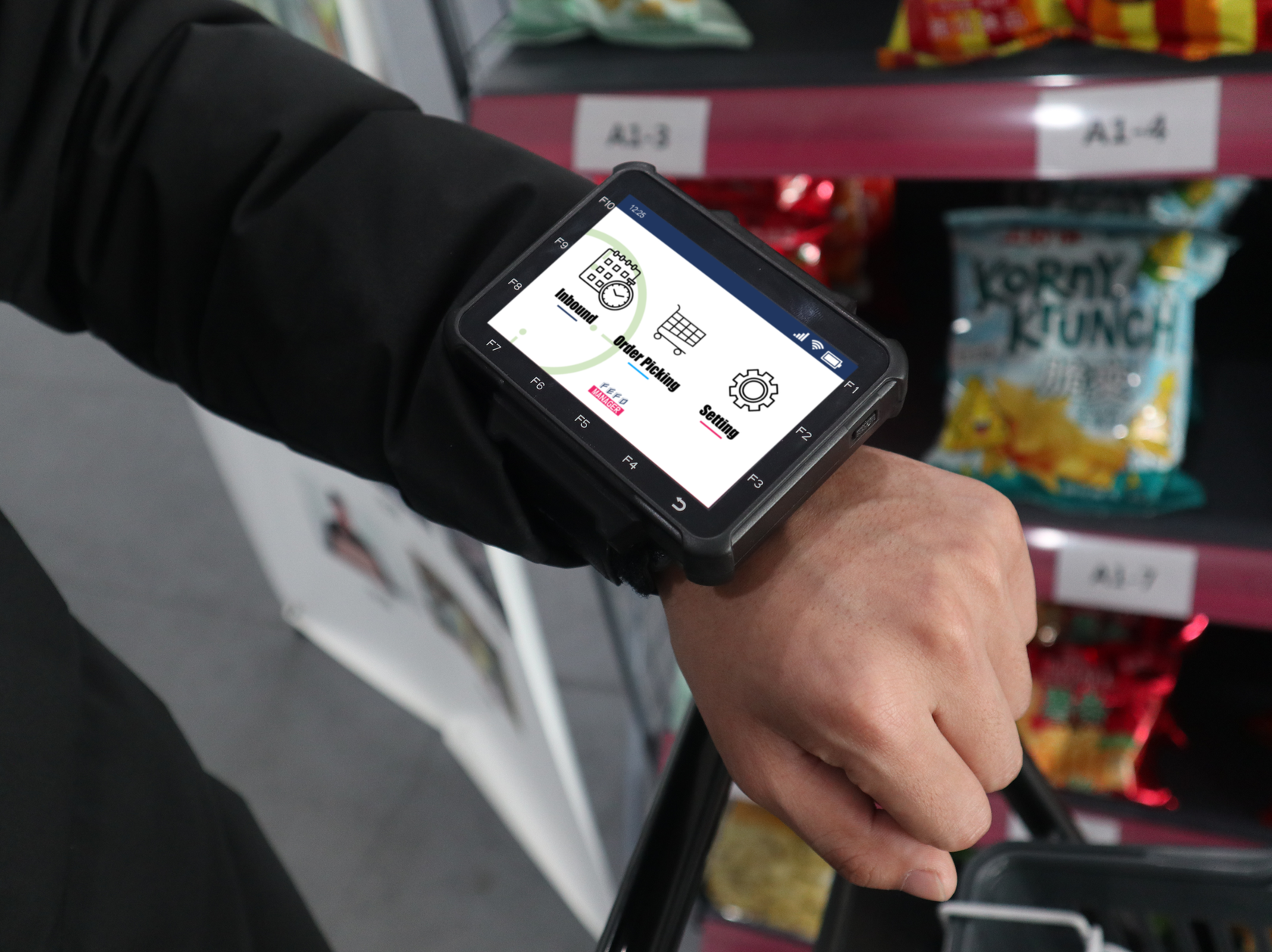
W563 Wearable Computer
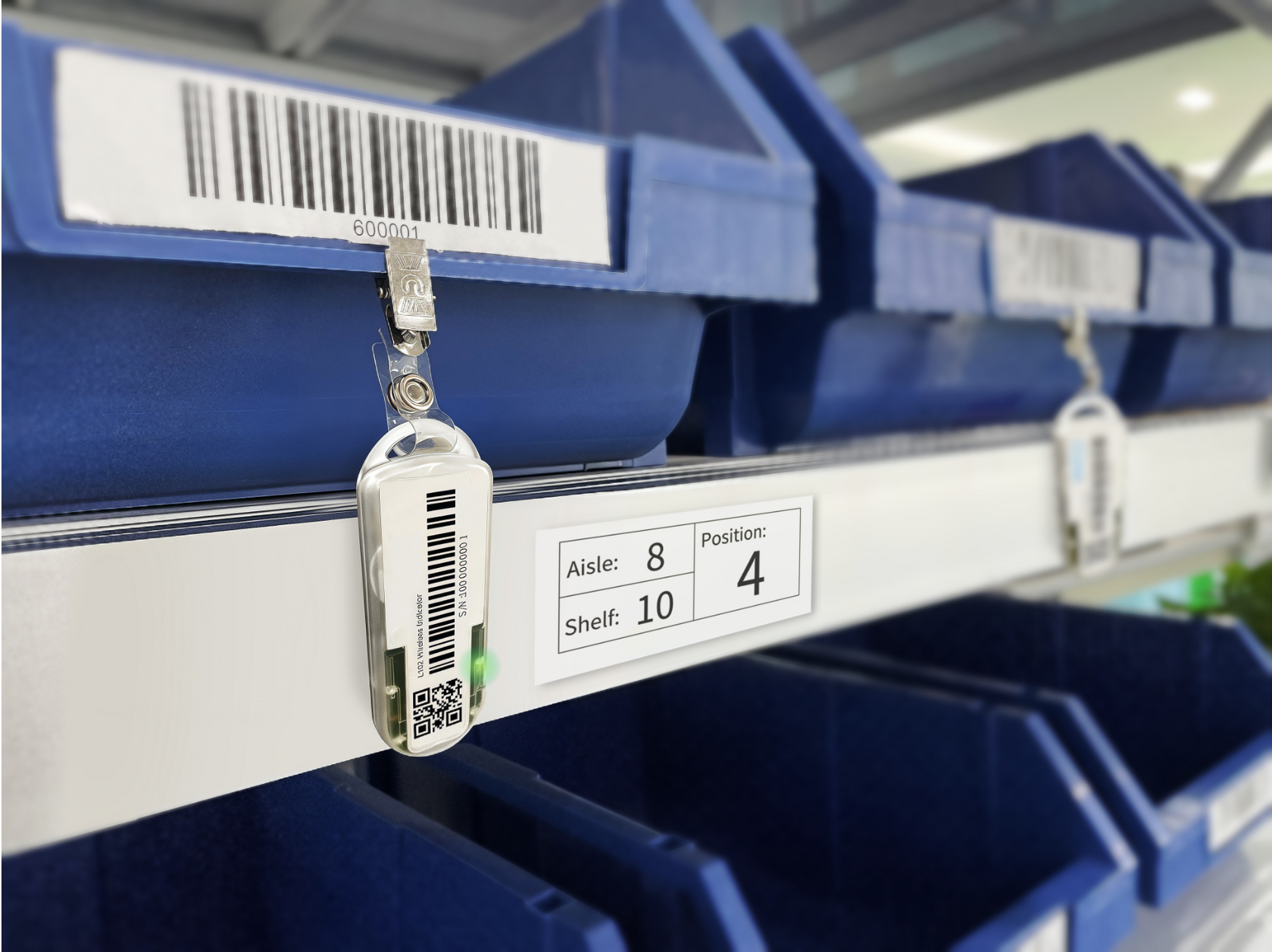
L102 Wireless Light Tag
Cost-effective FEFO for Small Companies
Small companies making or selling products with expiration dates have to be able compete in the market without risk. With our solution small companies can put into place an effective FEFO inventory strategy without bearing the huge expense of automation.